Create a loss prevention program
Written loss prevention programs, or workplace accident and injury reduction (AWAIR) programs, as they are officially called, promote safe and healthy conditions in the workplace.
Some states are required to have an AWAIR program and others are not. Regardless of whether it’s required, it’s a good idea for every organization to have one because it means you are clearly defining safety goals and making safety a priority for your employees.
Use our sample loss prevention program to get started (Word)
Six elements to include
When creating a loss prevention program, make sure to include the following six elements.
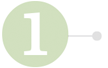
Your safety statement and objectives
This is to formalize management’s commitment to the safety and health of its employees.
- Include safety goals like reducing eye injuries or making sure staff properly operates equipment
- Specify steps to meet these goals, like requiring eye protection or providing training
- Clearly identify who is responsible for making these steps happen
- Explain how they will make it happen and how participation will be measured
Having a loss prevention program shows you are making safety a priority for your employees.

Work standards and rules
These are designed to regulate employee actions and define what is expected by management.
- Make them specific to your organization
- Include operating procedures for all equipment
- Include descriptions of previous accidents or those common in your industry with ideas on how to prevent them
- Review your rules each year and note any accidents that occurred
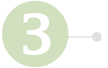
Enforcement procedures
Explain that all employees are expected and required to attend training and follow safety rules.
- Make it clear that not following the rules will result in disciplinary action
- Clearly define what warrants a verbal warning, written warning or termination
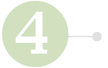
Employee training
Training new and current employees is essential.
- Teach safety skills
- Increase awareness of hazards and how to prevent accidents
- Create an understanding of work rules and operating procedures
- Develop an employee-management partnership that promotes safety
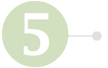
Worksite safety review and inspections
Develop processes to identify hazards and observe how employees work. This lets you test if your program is effective. Safety reviews let you look for:
- Potential hazards
- Workstation set-ups
- Work activities
- Modified work tasks
When doing reviews and inspections, try to eliminate hazards you note as best you can and modify procedures or workstations as needed.
Document everything including what you will do to follow up. Find out if past recommendations have been addressed and implemented.
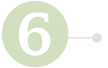
Reporting process and accident investigation
Even though you have a program in place, you might still have an accident. If it does:
- Make sure you report it to us right away
- Immediately investigate what happened and take action to prevent similar incidents in the future
Next steps
Once your formal written program is in place:
- Show support from the top by having the president of your organization sign the statement
- Make it available to all employees
- Let them know what is expected of them and of management
For help, contact your loss prevention representative or call (800) 937-1181.